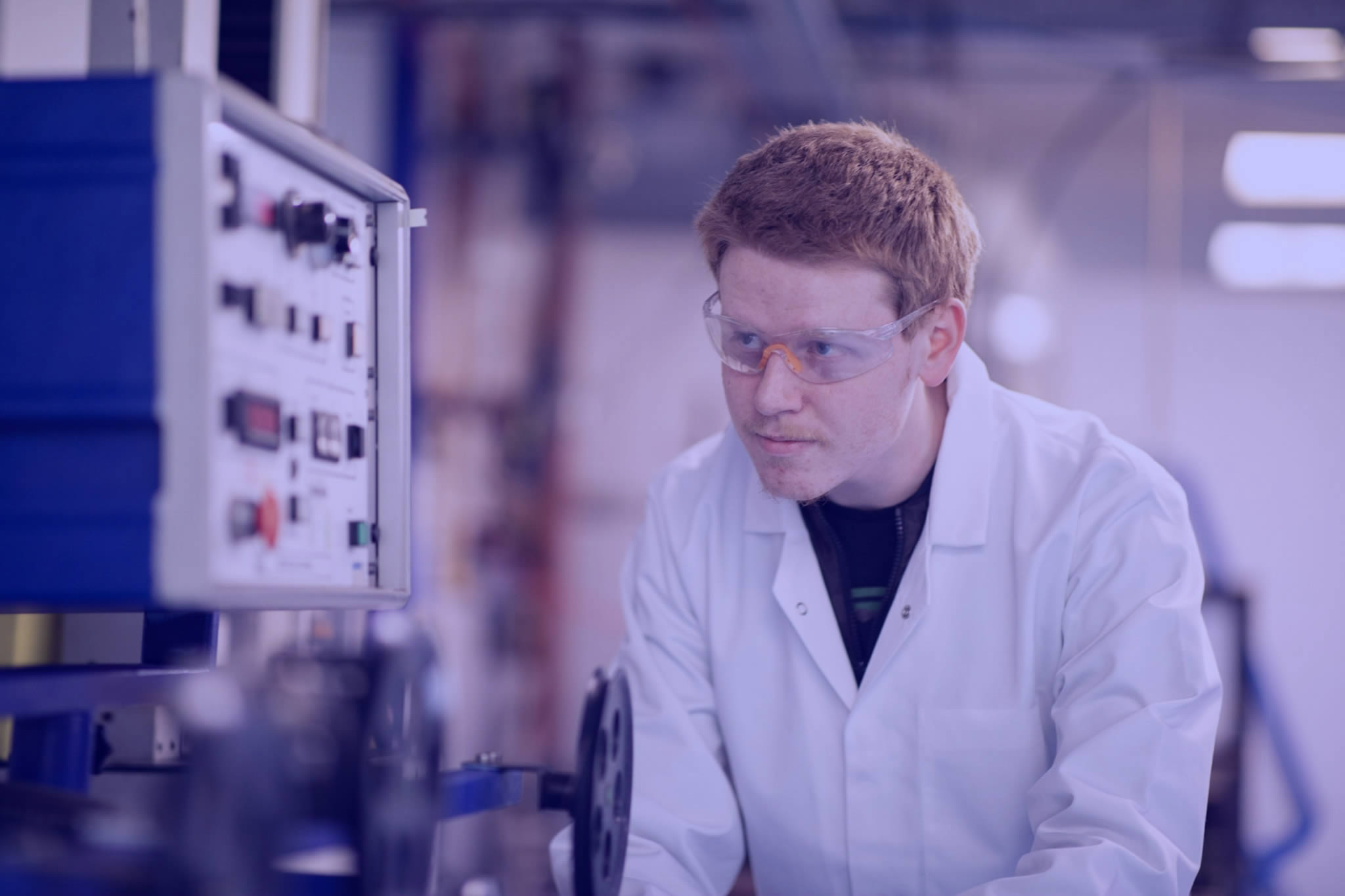
Transforming metals for a greener, brighter future
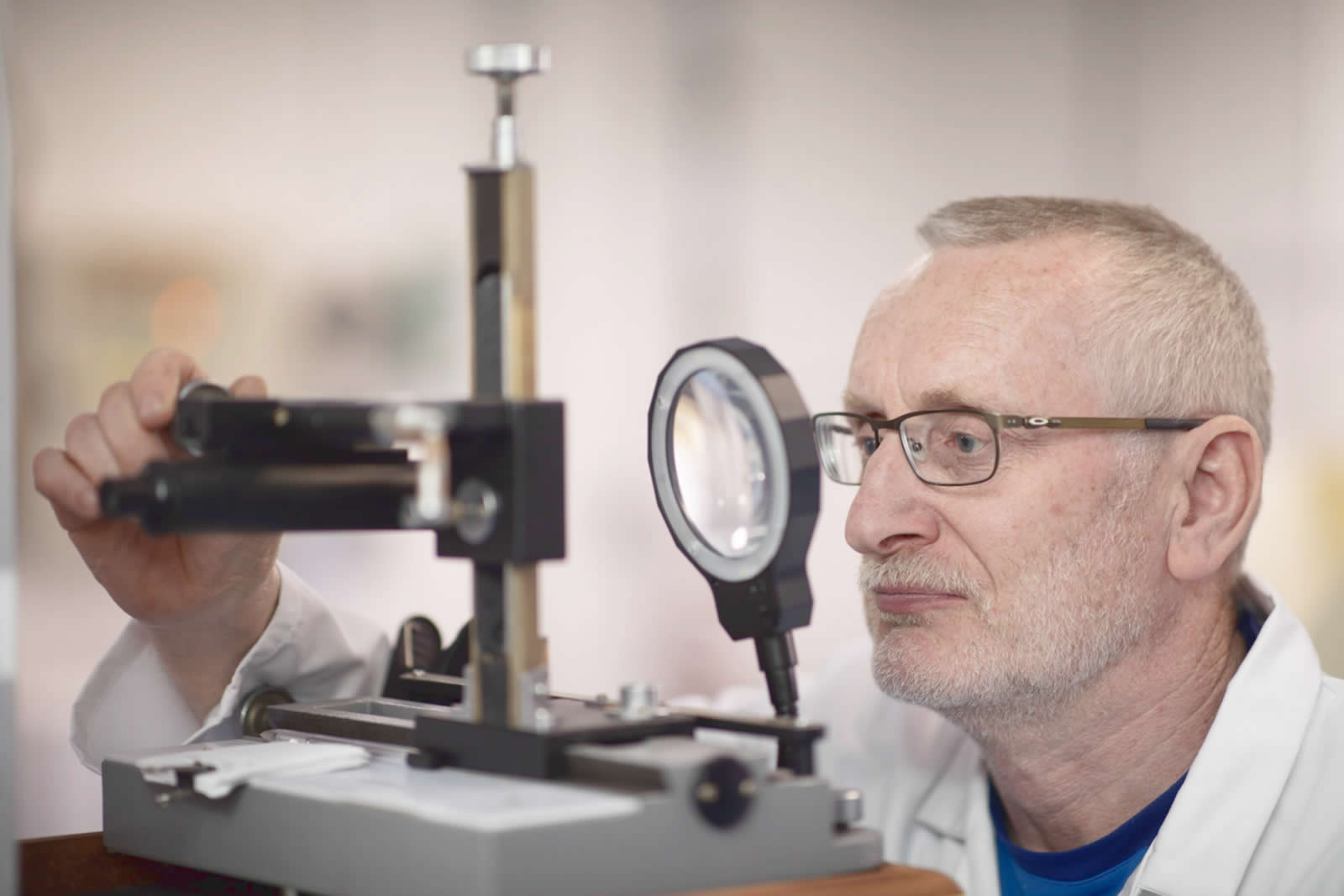
Rich Technology Heritage
TISICS' rich technology heritage began with BP Research in the 1990s to establish UK capability for high performance
fibre and metal composites.
Following transfer to QinetiQ in the late 90s futher developed aero gas turbine and landing gear component development
in close partnership with aerospace primes.
TISICS was founded in 2005 after acquiring the technology, to accelerate commercialisation in a range of industrial sectors.
Our Team
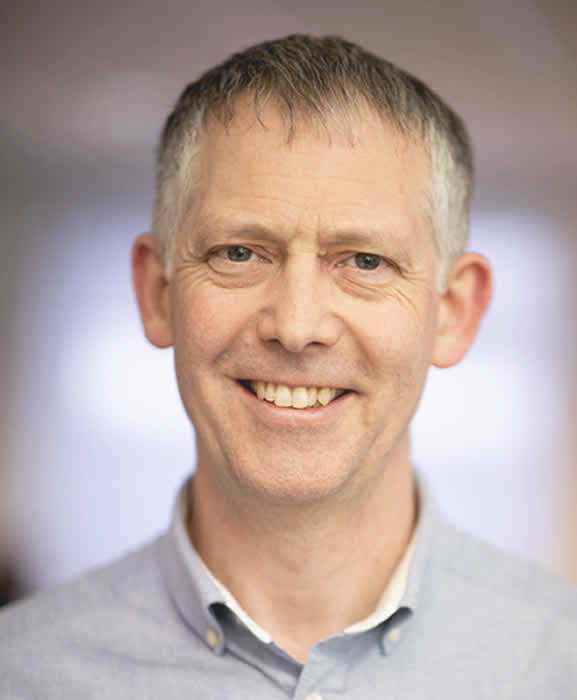
Stephen Kyle-Henney
CEO
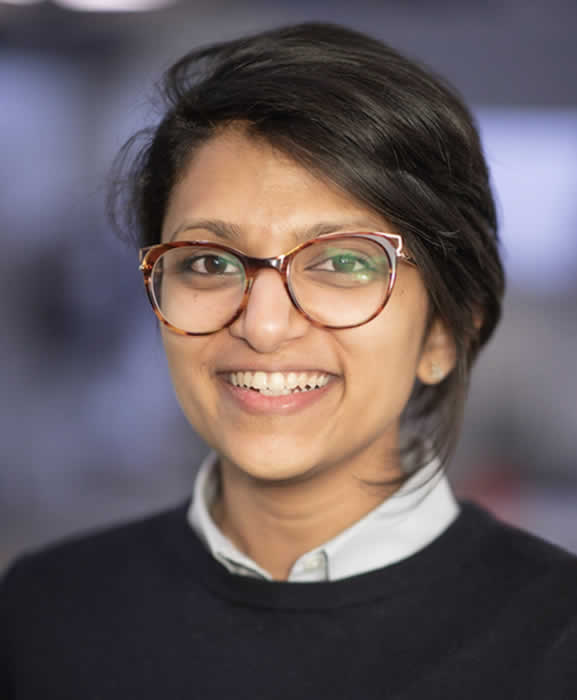
Ayantika Mitra
Business Strategy Director,
UKRI Future Leaders Fellow
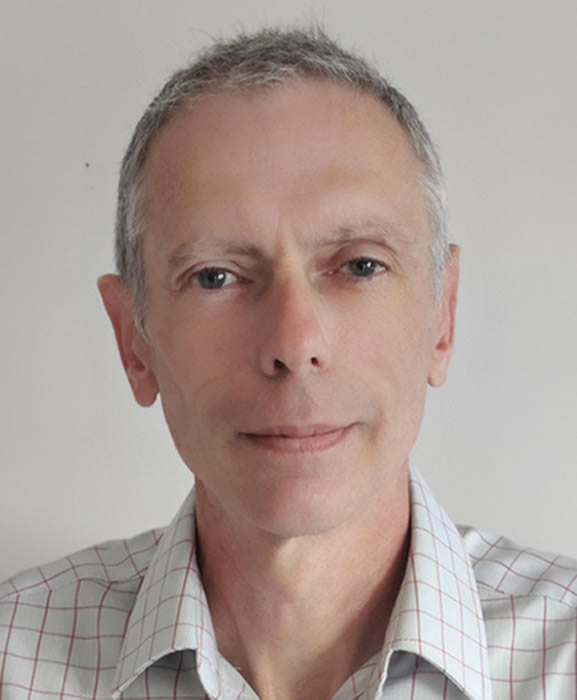
Colin Bennett
Chief Engineer
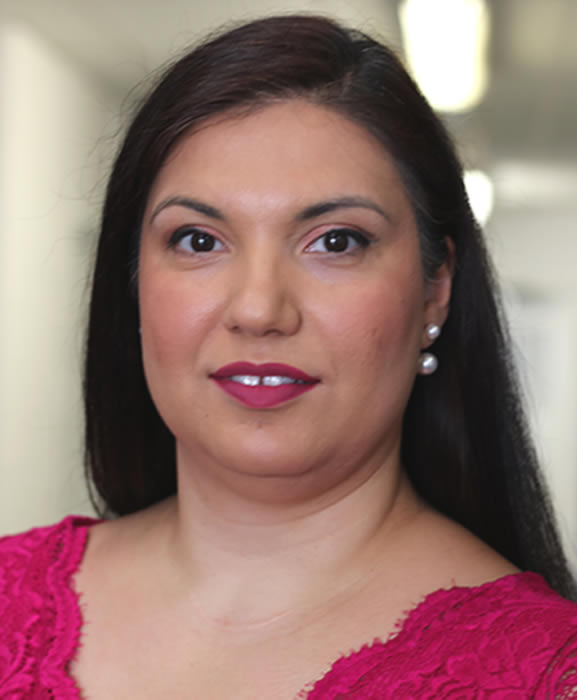
Eleni Mesaritis Daniel
Financial Controller
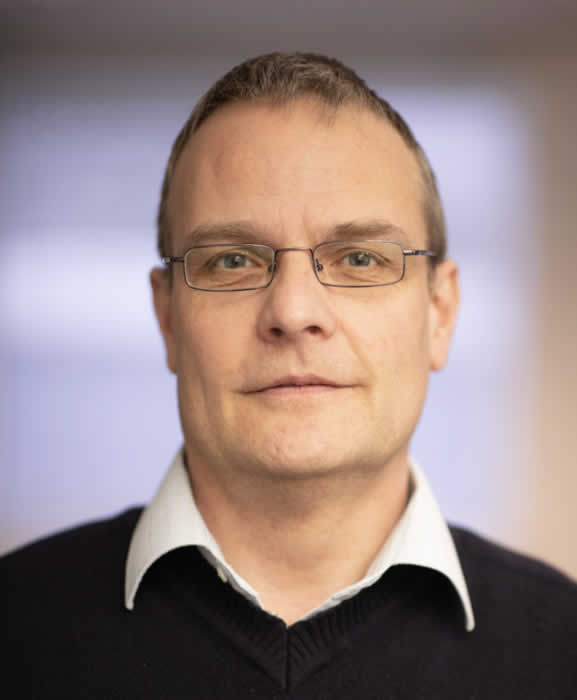
Dr Ralf Becker
Aerospace Systems Engineering Manager
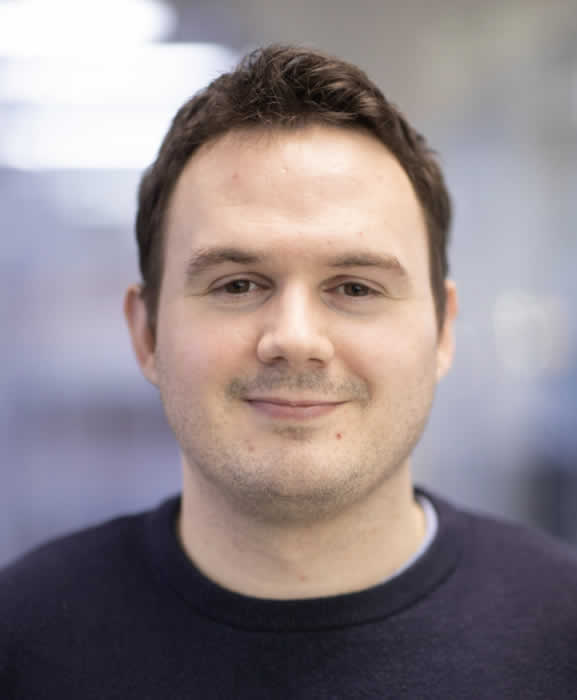
Craig Blacker
Composite Engineer
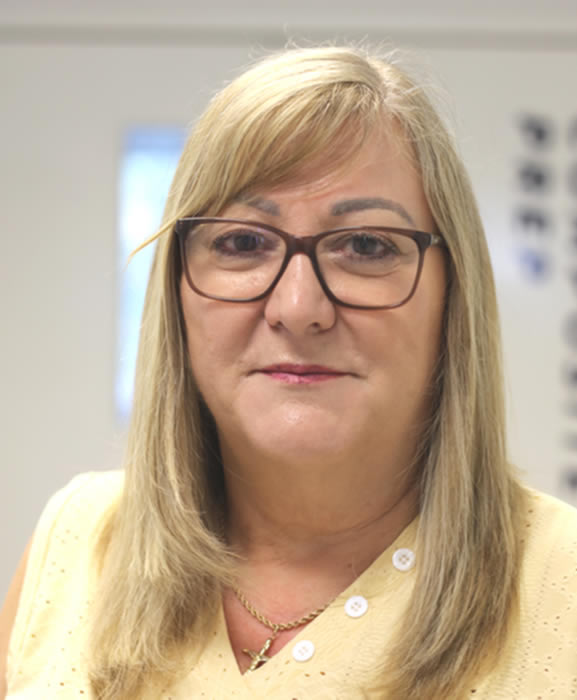
Janet May
Office Administrator
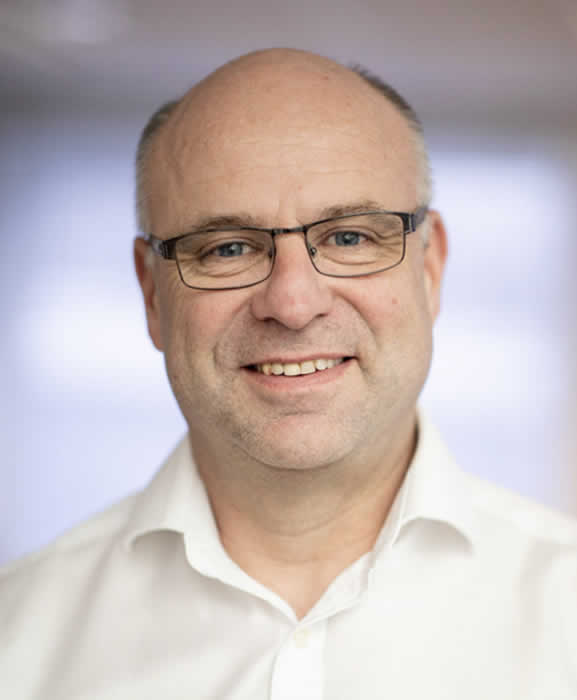
Mick Iles
Space Programmes Lead
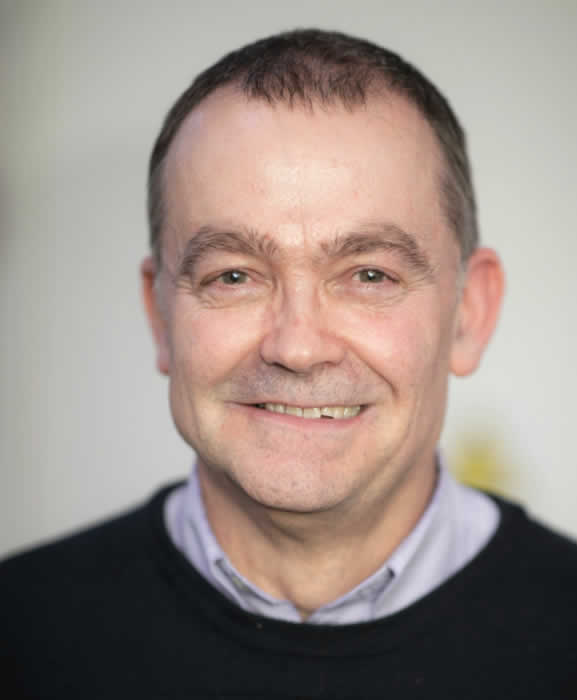
Dave Murgatroyd
Composite Design Lead
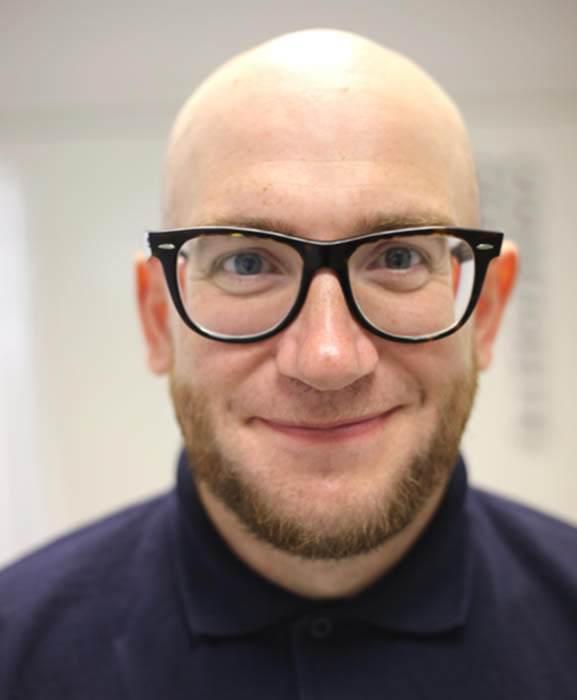
Phil Trussler
Fibre Technician
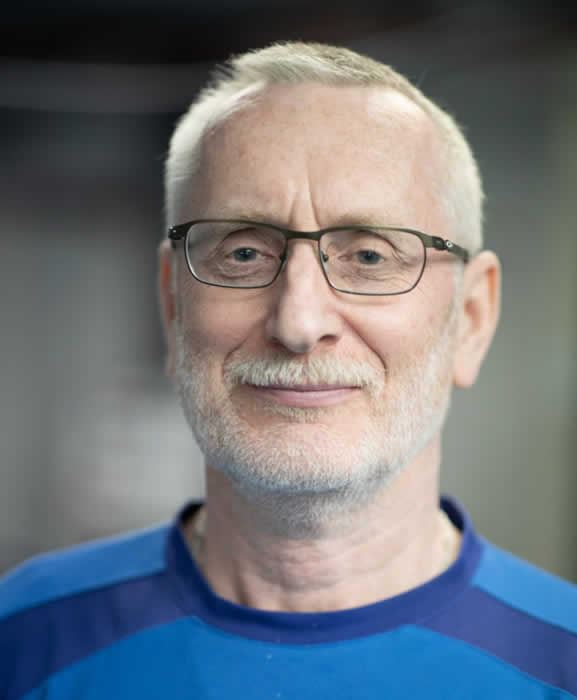
Ian Carmichael
Plant Engineer
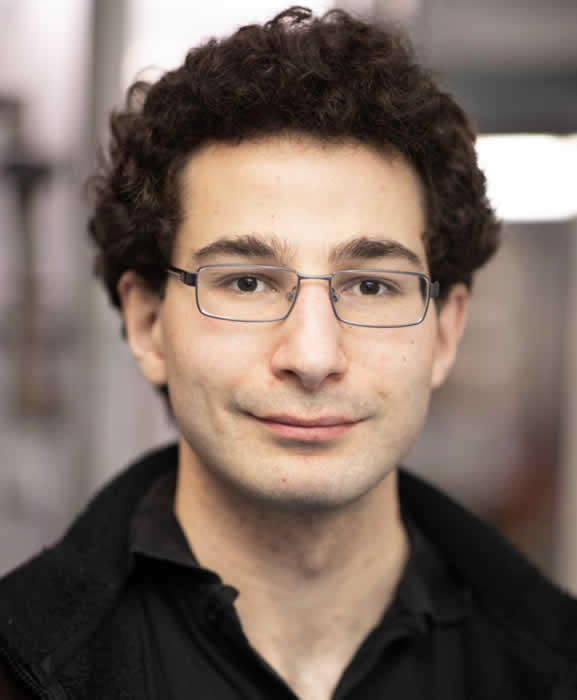
Dr Michael Rix
Technical Manager
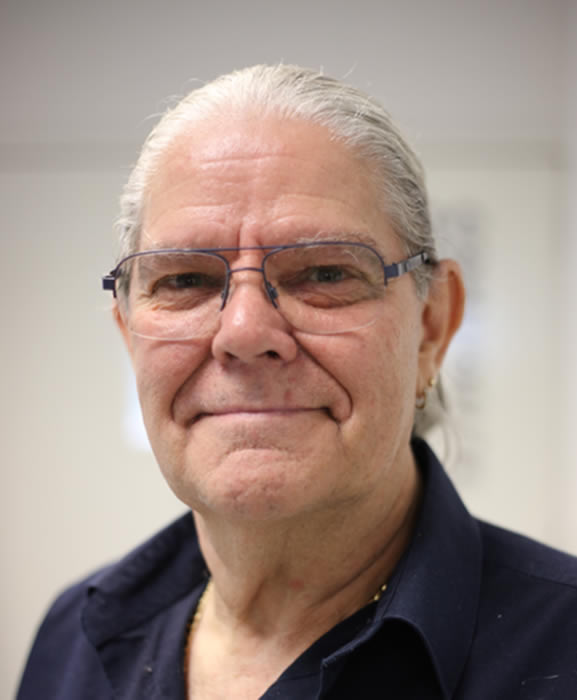
Gary Marwick
Workshop Manager
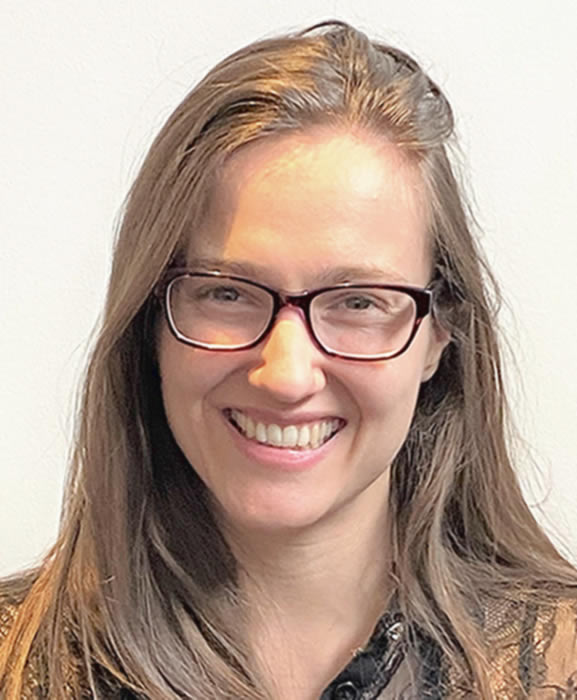
Laura Vieira
Accounts Assistant
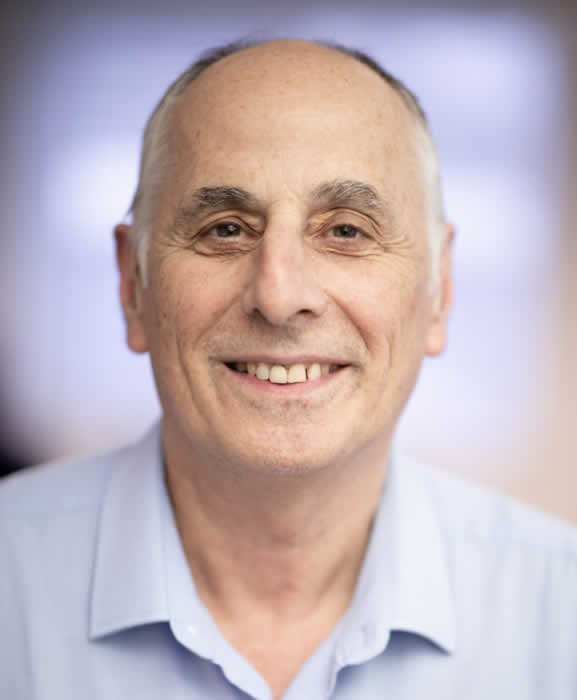